By Daniel Dunaief
One day, ships in the Navy may not only last longer in the harsh environment of salt water, but some of their more complicated parts may also be easier and quicker to fix.
That’s thanks to the mechanical engineering efforts of researchers at Stony Brook University and Brookhaven National Laboratory, who have been teaming up to understand the microstructural origins of corrosion behavior of parts they produce through laser additive manufacturing into shapes with complex geometries.
The Navy is funding research at the two institutions.
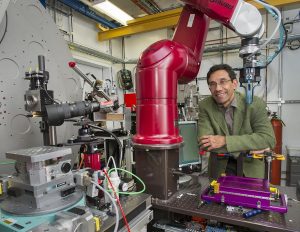
“As you would expect you’d need near any marine environment with salt water, [the Navy] is interested in laser additive manufacturing to enable the production of parts at lower cost that have challenging geometries,” said Jason Trelewicz, Associate Professor of Materials Science and Engineering at Stony Brook University. Additionally, the Navy is hoping that such efforts can enable the production of parts with specific properties such as corrosion resistance on demand.
“If you’re out at sea and something breaks, can you make something there to replace it?” asked Trelewicz. Ideally, the Navy would like to make it possible to produce parts on demand with the same properties as those that come off a manufacturing line.
While companies are currently adopting laser additive manufacturing, which involves creating three-dimensional structures by melting and resolidfying metal powders one layer at a time with the equivalent of a laser printer, numerous challenges remain for developing properties in printed materials that align with those produced through established routes.
Additive materials, however, offer opportunities to structure products in a way that isn’t accessible through traditional techniques that create more complex geometry components, such as complex heat exchangers with internal cooling channels.
In addition to the science remaining for exploration, which is extensive, the process is driving new discoveries in novel materials containing unique microstructure-chemistry relationships and functionally graded microstructures, Trelewicz explained.
“These materials are enabling new engineering components through expanded design envelopes,” he wrote in an email.
With colleagues from BNL including Research Associate Ajith Pattammattell and Program Manager for the Hard X-ray Scattering and Spectroscopy Program Eric Dooryhee, Trelewicz published a paper recently in the journal Additive Manufacturing that explored the link between the structure of the material and its corrosive behavior for 316L stainless steel, which is a corrosion resistant metal already in wide use in the Navy.
The research looked at the atomic and microstructure of the material built in the lab of Professor Guha Manogharan at Penn State University. Working with Associate Professor Gary Halada in the Department of Material Science and Chemical Engineering, Trelewicz studied the corrosive behavior of these materials.
Often, the surface of the material went through a process called pitting, which is common in steels exposed to corrosive environments, which occurs in cars driven for years across roads salted when it snows.
The researchers wanted to understand “the connection between how the materials are laser printed, what their micro structure is and what it means for its properties,” Trelewicz said, with a specific focus on how fast the materials were printed.
While the research provided some structural and atomic clues about optimizing anti corrosive behavior, the scientists expect that further work will be necessary to build more effective material.
In his view, the next major step is understanding how these defects impact the quality of this protective film, because surface chemical processes govern corrosive behavior.
Based on their research, the rate at which the surface corrodes through laser additive manufacturing is comparable to conventional manufacturing.
Printed materials, however, are more susceptible to attack from localized corrosion, or pitting.
At the hard x-ray nanoprobe, Pattammattel explored the structure of the material at a resolution far below the microscopic level, by looking at nonstructural details.
“It’s the only functional beamline that is below 10 nanometers,” he said. “We can also get an idea about the electronic structures by using x-ray absorption spectroscopy,” which reveals the chemical state.
Pattammattel, who joined BNL in 2018, also uses the beamline to study how lung cells in mice interact with air pollutants. He described “the excitement of contributing to science a little more” as the best part of each day.
Meanwhile, Dooryhee as involved in writing the seed grant proposal. By using the x-rays deflected by the variety of crystalline domains or grains that compose the materials, HE can interpret the material’s atomic structure by observing the diffraction angles. The discrete list of diffraction angles is a unique fingerprint of the material that relates to its long-range atomic ordering or stacking.
In this study, researchers could easily recognize the series of diffraction peaks associated with the 316L stainless steel.
Dooryhee was able to gather insight into the grain size and the grain size distribution, which enabled him to identify defects in the material. He explained that the primary variable they explored was the sweeping rate of the laser beam, which included 550, 650 and 700 millimeters per second. The faster the printing, the lower the deposited energy density.
Ultimately, Dooryhee hopes to conduct so-called in situ studies, in which he examines laser additive manufacturing as it’s occurring.
“The strength of this study was to combine several synchrotron techniques to build a complete picture of the microstructure of the [additively manufactured] material, that can then be related to its corrosion response,” he explained in an email.
Dooryhee grew up in Burgundy France, where his grandfather used to grow wine. He worked in the vineyards during the fall harvest to help pay for his university studies. Dooryhee has worked at BNL for over 12 years and appreciates the opportunity to collaborate with researchers at Stony Brook University.